تشخیص میلگرد تقلبی و اصل
تشخیص میلگرد تقلبی و اصل
در عصر حاضر، صنعت فولاد و آهن و تولیدات آهنی و فلزی در تمامی صنایع مانند، کشتی سازی، نظامی، پزشکی، ساختمان سازی و … مورد استفاده قرار میگرد به همین سبب همواره شاهد افزایش تعداد کارخانجات تولیدی انواع مقاطع و ورق های فولادی می باشیم. به دلیل وجود سود سرشار در این بازار، افراد سودجو نیز به فکر کسب منافع خود بوده و با وارد کردن محصولات تقلبی قصد کسب سود بیشتری را دارند.
پایین بودن قیمت میلگرد ، قیمت تیرآهن و … یک شرکت ممکن است شما را وسوسه کند ولی این مطلب مورد اهمیت است که استفاده از محصولات بی کیفیت و تقلبی باعث ضررهای جبران ناپذیری می شود. برای مثال استفاده کردن از میلگرد تقلبی در ستون های یک برج می تواند در هنگام زلزله باعث تخریب کامل و ضررهای جانی و مالی جبران ناپذیری شود، به همین دلیلی خریداران بایستی پیش از خرید نسبت به اصل یا تقلبی بودن این محصولات اطمینان یابند. در زیر نکات مهمی برای تشخیص میلگرد تقلبی و اصل گرداوری شده است.
علائم اختصاری میلگرد
از آن جا که هر کارخانه ای دارای علامت اختصاری و مشخصاتی بر روی محصولات خود می باشد، هنگام خرید میبایست به این علایم توجه کنید تا از خرید محصولات تقلبی و جعلی در امان باشید. علامت های حک شده روی بدنه میلگرد آجدار جدای از مشخص نمودن نام کارخانه، ممکن است روش تولید آن را نیز نشان دهد. توجه داشته باشید این علامت باید به صورت برجسته روی بدنه حک شده باشد. حک شدن علایم با سنبه و موارد از این دست که به صورت دستی انجام می شود خود گواه بر تقلبی بودن بار محسوب می شود.

علامت اختصاری میلگرد فایکو
برای مثال :
SA : میلگرد آجدار ۵۰۰ ، روش تولید: آلیاژی ، نوع آج: آجدار مرکب
CT: میلگرد آجدار ۴۰۰ ، روش تولید: ترمکس (خنک کاری) ، نوع آجد: آجدار جناغی
CU : میلگرد آجدار ۴۰۰ ، روش تولید: آلیاژی ، نوع آج: آجدار جناغی
T :میلگرد آجدار ۳۶۰ ، روش تولید: ترمکس (خنک کاری) ، نوع آج: آجدار مارپیچ
JU : میلگرد آجدار ۳۴۰ ، روش تولید: آلیاژی ، نوع آج: آجدار مارپیچ
اعداد ۵۰۰،۴۰۰ و ۳۴۰ بیانگر حداقل میزان تنش کششی میلگرد در حالت تسلیم است. برای مثال بر روی میلگردی NFG CO UJ درج شده است. NFG نام شرکت تولیده کننده (مجتمع فولاد نورد گیلان) و UJ یعنی دارای آج مارپیچ با تنش ۳۴۰ و نوع A3 است.
به طور کلی شیوه علامت گذاری میلگردها به این صورت است که از سمت چپ نشان یا نام شرکت تولیدکننده می باشد . پس از آن کد مربوط به مشخصه و در نهایت کد مربوط به فرآیند تولید آن می باشد. برای مثال علامت اختصاری IAS CO بر روی یک میلگرد، سه حرف IAS نشان دهنده شرکت تولیدی فولاد آلیاژی ایران، حرف C نشان دهنده مشخصه میلگرد آجدار جناغی آج 400 بوده که همان میلگرد A3 می باشد و حرف U نشان دهنده تولید میلگرد به روشی غیر از ترمکس می باشد.
پلاک شناسایی
یکی از ساده ترین و سطحی ترین روش شناخت میلگرد وجود پلاک های نصب شده بر روی بندل می باشد. این پلاک نماد و هویت محصول را معرفی می کند و به صورت ورق فلزی یا برچسب روی محصول نصب می گردد. بر روی این پلاک مواردی نظیر تاریخ تولید، شماره شناسایی محصول، وزن بندل، گرید، استانداردهای کسب شده و … درج می شود که خریداران می توانند به صورت فوری از این ویژگی ها مطلع شوند.

پلاک شناسایی میلگرد عتیق آذر سهند
وزن میلگرد
جدول اشتال میلگرد مرجع وزنی برای این محصول به شمار می رود. معمولا کارخانجات معتبر نظیر ذوب آهن اصفهان محصولات خود را منطبق بر جدول وزن اشتال تولید می کنند. میلگردهای متفرقه در هر شاخه اختلاف وزنی زیادی با نمونه استاندارد دارند. هرچند خریداران به دنبال محصول سبک تر هستند تا بهای کمتری پرداخت کنند اما شاخص وزن یکی از استانداردهای مهم در آهن آلات محسوب می شود که نباید به بهانه ارزانی آن را نادیده گرفت.

مقایسه وزنی میلگرد های مطرح بازار
رنگ میلگرد
اصولا میلگرد مرغوب که از کارخانه خارج می شود به رنگ تیره و مشکی می باشد. در نظر بگیرید که رنگ میلگرد ممکن است بر اثر رطوبت و آب باران به زرد تغییر کند. این رنگ همان زنگار است که اگر در مدت کوتاه صورت گرفته باشد و در عمق پروفیل وارد نشده باشد خللی در کار ایجاد نمی کند. قبلا پدیده زرد شدن آهن طی نوشتاری توضیح داده شده است.
خرید میلگرد متفرقه ایرادات دیگری نیر دارد. در هر بندل میلگرد متفرقه و نا معلوم امکان وجود میلگرد نرمال و کمتر از 12 متر وجود دارد.
برگ آنالیز میلگرد
هر محصول فولادی که استاندارد باشد برگه ای تخت عنوان برگ آنالیز به همراه خود دارد که مشتری در هنگام خرید می تواند آن را رویت نماید. این برگه آزمون کوانتومتری و تاییده آزمایشگاهی می باشد که شامل درصد ترکیبات میلگرد است. مواردی همچون استحکام کششی، ازدیاد طول و وزن دقیق نیز شامل این آنالیز است. محصولات معتبر و استاندارد حتما چنین برگه ای در هنگام خرید دارند و خریدار می تواند آن را از فروشنده درخواست کند. برگ آنالیز محصول از مهمترین روش های تشخیص میلگرد تقلبی و اصل است.
در نظر بگیرید که میلگرد ساختمانی مرغوب تا 90 درجه به صورت مکانیکی و سرد خمکاری می شود.

نمونه برگ آنالیز میلگرد نیشابور
خرید از شرکت های معتبر
مهمترین مسئله در خرید میلگرد رجوع به فروشگاه یا شرکت های مطمئن و با سابقه است. طبیعتا مغازه های خرده فروشی امکان تهیه صورت های سنگین آهن آلات را ندارند و به دلیل وجود حاشیه سود بالا در این خریدها امکان قرار دادن بار نامرغوب در لابلای بندیل ها وجود دارد.
شرکت نگین فولاد السا با قریب دو دهه سابقه در بازار آهن آلات و با کادری مجرب به شما مشتریان گرامی این اطمینان خاطر را می دهد که کلیه مقاطع فولادی از معتبرترین برندها و منطبق با درخواست خرید شما تحویل داده شود.
تفاوت آهن و چدن چیست
تفاوت آهن و چدن و روش های تشخیص آن
چندن ها و آهن ها با یکدیگر تفاوت های بسیاری از نظر خواص و مواد تشکیل دهنده دارند که در زیر به برخی از این تضاد ها می پردازیم. پیش تر نیز به تفاوت آهن و فولاد طی نوشتاری پرداخته شده بود.
چدن چیست ؟
چدن (Cast Irons) خانواده ای از آلیاژهای آهنی هستند که از آهن، کربن (از ۲٫۱۱٪ تا تقریباً ۴٫۵٪) و سیلیسیم (تا ۳٫۵٪) تشکیل میشوند . چدنها غیر از نوع داکتیل ، تا حدودی شکننده هستند و به دلیل داشتن نقطه ذوب پایین، سیالیت بالا، قابلیت ریختهگری آسان، قابلیت ماشین کاری بالا، تغییرشکل ناپذیری و مقاومت به سایش بالا، به موادی مهندسی با دامنه وسیعی از کاربردها تبدیل شدهاند و در تولید انواع لولهها، ماشین آلات، قطعات مورد استفاده در صنعت خودروسازی مانند سرسیلندر، بلوک سیلندر و جعبه دنده به کار میروند. چدنها همچنین در برابر تخریب ناشی از اکسایش و زنگ زدگی مقاومت بالایی دارند.
تولید چدن
چدن از طریق ذوب مجدد سنگ آهن به همراه آهن و فولاد قراضه بدست میآید و با طی مراحلی برای حذف عناصر ناخواسته مانند فسفر و گوگرد همراه است. بسته به نوع کاربرد، میزان کربن و سیلیسیم تا حد مطلوب (به ترتیب ۲ تا ۳٫۵ و ۱ تا ۳ درصد وزنی) کاهش داده میشوند. سایر عناصر نیز حین ریختهگری و قبل از شکلگیری نهایی، به مذاب افزوده میشوند. چدن به جز موارد خاص که در کوره بلند موسوم به کوره کوپل ذوب میشود، عمدتاً در کورههای القای الکتریکی تولید میگردد. پس از تکمیل ذوب، مذاب به کوره نگهدارنده یا قالب ریخته میشود.
در اواخر قرن ۲۰ میلادی ، ظروف نچسب بیشتر از چدن در بیشتر خانه ها رایج شده بود ، آشپزهای بیشتری به استفاده از قابلمه های چدنی برگشتند و این آلیاژ را به عنوان یک گزینه مناسب و سالم انتخاب کردند و مزایای آن را دوباره کشف کردند. چدن آلیاژی از آهن و کربن است که در آن بیش از ۲% کربن وجود دارد. این آلیاژ به دلیل مقرون به صرفه بودن و دوام بالا ، تا اوایل قرن ۲۰ ماده مورد علاقه ظروف آشپزی بود. این ماده از آلومینیوم ارزان تر بود و به طور گسترده تری در دسترس مردم قرار می گرفت .
بسته به محتوای سیلیکون موجود در چدن، این ماده به عنوان چدن سفید یا چدن خاکستری طبقه بندی می شود و ممکن است تحت دمای بیشتر تحت فرآوری قرار گیرد تا چدن قابل انعطاف یا شکل پذیر تولید شود.
دسته بندی چدنها
اولین طبقهبندی انجام شده برای چدنها در گذشته بر اساس رنگ سطح مقطع شکست آنها انجام گرفت. بر این اساس چدنها به دو دسته کلی تقسیم شدند
چدن سفید: از آنجا که در این چدنها، شکست در امتداد صفحات کاربید آهن رخ میدهد، سطح مقطع شکست کریستالی آنها سفید است.
چدن خاکستری: در این چدنها، شکست در امتداد صفحات گرافیت رخ میدهد، به همین دلیل سطح مقطع شکست کریستالی آنها خاکستری است.
کاربرد چدن
- در تولید قطعات ریختگی تحت فشار از جمله شیر فلکه ها، بدنه های پمپ قطعات ماشین آلات که در معرض شوک و خستگی هستند، میل لنگ ها، چرخ دنده ها، غلتک ها، تجهیزات فرایند شیمیایی، مخازن ریختگی تحت فشار و…
- برای خودرو و صنایع وابسته به آن مثلا در ساخت مفصل های فرمان، دیسک ترمزها، بازوها، میل لنگها و چرخ دندهها، صفحه کلاچها و…
- در راه آهن، کشتیرانی و خدمات سنگین و دیگر جاهایی که نیاز به مقاومت در برابر شوک است مثلا در تجهیزات الکتریکی کشتیها، بدنه موتور، پمپ ها، بست ها و غیره.
- قطعات غیر فشاری برای کاربردهای درجه حرارت بالا برای مثال در ساخت قطعات و جعبه های درگیر با آتش، میله های شبکه، قطعات کورهها، قالبهای شمش، قالبهای شیشه، بوتههای ذوب فلز.
- اگر چدن های غیر آلیاژی به طور کلی مقاوم به خوردگی ( Corrosion ) بویژه در محیط های قلیایی هستند، مهمترین کاربرد این چدنها در پمپهای دندهای حمل اسید سولفوریک، پمپها و شیرهایی که در آب دریا مصرف میشوند، قطعات مورد استفاده در سیستم های بخار و جابجایی محلول های آمونیاکی، سود و نیز برای پمپاژ و جابجایی نفت خام اسیدی در صنایع نفت هستند.

ظروف آشپزخانه چدنی
آهن چیست ؟
آهن ( Fe ) نام یک عنصر شیمیایی با عدد اتمی ۲۶ و چگالی ۷۸۷۴ کیلوگرم بر مترمکعب است. آهن یک فلز است که در نخستین دوره فلزهای واسطه جای دارد. آهن از دیدگاه جرم، بزرگترین عنصر سازنده کره زمین است. آهن اصلیترین عنصر سازنده هسته بیرونی و درونی زمین و چهارمین عنصر متداول در پوستهاست.
در حدود 1400 پیش از میلاد، از ساختههای آهنی در قلمرو هیتیها در ارمنستان کنونی استفاده میشد که این به عنوان نخستین شواهد مصرف این عنصر است.
تولید آهن فلزی
الف) روشهای آزمایشگاهی
در برخی کاربردهای خاص که به آهن خالص نیاز است میتوان آن را در آزمایشگاه در مقادیر کم از طریق کاهش اکسید خالص یا هیدروکسید آن با هیدروژن تولید کرد، یا میتوان پنتاکربونیل آهن را تا ۲۵۰ درجه سلسیوس گرم کرد تا تجزیه شده و آهن خالص پودری ایجاد گردد. روش دیگر الکترولیز کلرید آهن بر روی کاتد آهنی است.
ب) روشهای صنعتی اصلی
سنگ آهن
امروزه، تولید صنعتی آهن یا فولاد از دو مرحله اصلی تشکیل شدهاست. در مرحله اول، سنگ آهن با کک در کوره بلند کاهش یافته و فلز مذاب از ناخالصیهایی مانند کانیهای سیلیکات جدا میشود. در این مرحله آلیاژی تولید میشود – آهن خام – که حاوی مقادیر نسبتاً زیادی کربن است. در مرحله دوم، توسط فرایند اکسایش مقدار کربن موجود در آهن خام کاهش مییابد تا آهن فرفورژه، فولاد یا چدن تولید شود. در این مرحله میتوان سایر فلزات را برای ساخت آلیاژهای فولادی به آن اضافه کرد.
کاربرد آهن
مصارف آهن آلات شامل صنعتی و ساختمانی می باشد. برای ساختمان سازی آهن را به اشکال مختلف نوردکاری می کنند که اصطلاحا پروفیل های ساختمانی نامیده می شود. تیرآهن ، میلگرد، نبشی، ناودانی و انواع ورق آهنی جزو پرکاربردترین مقاطع آهنی محسوب می شوند.
در صنعت نیز آهن به اشکال مختلف به کار گرفته می شود و به کمک جوشکاری، پرچ و پیچ به یکدیگر اتصال داده می شود. امروزه کمتر پیشه و صنعتی وجود دارد که در آن آهن استفاده نشود.

آمار تولید سنگ آهن کشورها بین سالهای 2015 تا 2018

میزان تولید کنسانتره سنگ آهن در کشور
تفاوت آهن و چدن چیست و روشهای تشخیص
آهن: آهن از فولاد کم کربن تولید می شود. کیفیت این نوع آلیاژ توسط درصد کربن و منگنز پایین مشخص می گردد. (کربن کمتر از ۰.۰۸ درصد و منگنز کمتر از ۰.۰۶ درصد)
چدن: چدن آلیاژي از آهن و کربن است که عموما ۳ تا ۵ درصد کربن و ۱ تا ۳ درصد سیلیسیم دارد. میزان کربن چدن، از فولاد بیشتر است. چدن ها گروه مهمی از آلیاژهای ریخته گری هستند.
- نقطه ی ذوب چدن پایین تر از نقطه ذوب آهن است.
- چدن نسبت به آهن در مقابل خوردگی آسیب پذیر تر می باشد.
- چدن بسیار خشک تر و خمش ناپذیرتر از فولاد و آهن می باشد.
- نگاه کردن به سطح دو فلز : سطح فلز آهن به رنگ خاکستری تیره و براق می باشد. فلز چدن ( چه چدن سفید چه چدن خاکستری) سطحی مات و کدر و رنگی خاکستری دارد.
- تست جرقه (Spark Test) : در صورت وجود دستگاه سنگ رو میزی تست جرقه (Spark Test) را انجام می دهیم. با قرار دادن لبه ای از دو فلز زیر سنگ رومیزی و نگاه کردن به جرقه آن می توان تا حدی به ماهیت آن دو فلز پی برد.
- اگر طول جرقه ها کم ، رنگ آن قرمز ، و نوک جرقه ها برفکی شکل باشد فلز چدن است.
- اگر طول جرقه ها زیاد، رنگ آن سفید، و نوک جرقه ها چنگالی و سوزنی شکل باشد فلز آهن (فولاد کم کربن) است.
- تست براده : چدن فلزی ترد است. پس براده ی آن نیز ترد و شکننده است. در صورت وجود دستگاه تراش یا فرز می توانیم قسمتی از یک نمونه فلز را ماشینکاری کنیم. اگر براده ناپیوسته باشد فلز چدن و اگر براده پیوسته باشد فلز آهن است. برای انجام این تست حتما نیازی به دستگاه تراش یا فرز نیست. با یک قلم تیز نیز می توان این آزمایش را انجام داد. به طوری که سعی کنیم یک لایه ی نازک از روی فلز برداریم. اگر لایه مانند نوار برداشته شد فلز آهن و اگر براده ها بسیار ریز برداشته شدند. فلز چدن است.
- رنگ فلز ذوب شده آنها : نمونه را زیر مشعل قرار داده و تا رسیدن به نقطه ذوب صبر می کنیم. در لحظه ذوب شدن رنگ فلز می تواند در تشخیص نوع آن به ما کمک کند. اگر رنگ فلز گداخته شده قرمز باشد، فلز چدن است. اگر رنگ فلز گداخته شده سفید باشد، فلز آهن است.
پر مصرف ترین سایز تیرآهن در کشور
از ساخت سازه های مسکونی تا سوله های صنعتی و جاده سازی گستره مصرف تیرآهن محسوب می شود. تیرآهن مقطعی شبیه به حرف I یا H لاتین می باشد که برای ساخت استراکچر بنا و انواع سازه ها نظیر پل استفاده می شود. وظیفه اصلی تیرآهن تحمل نیروهای تنشی و خمشی وارد بر سازه است.
تولید کنندگان تیرآهن در ایران
کارخانجات متعددی در ایران این مقطع فولادی را در خط تولید خود ذوب ریزی و نورکاری می کنند. ماهان در شهر سمنان، گروه ملی اهواز، ناب تبریز، فایکو در شهر ساری و ظفر بناب، نورد آریان فولاد، شاهین بناب از تولید کنندگان مطرح تیر آهن محسوب می شود. البته در این بین شرکت ذوب آهن اصفهان بالاترین تیراژ تولید در کشور را دارد. محصولات این شرکت را در بازار به اصطلاح تیرآهن ذوبی می نامند.
تفاوت تیرآهن هاش با تیرآهن معمولی
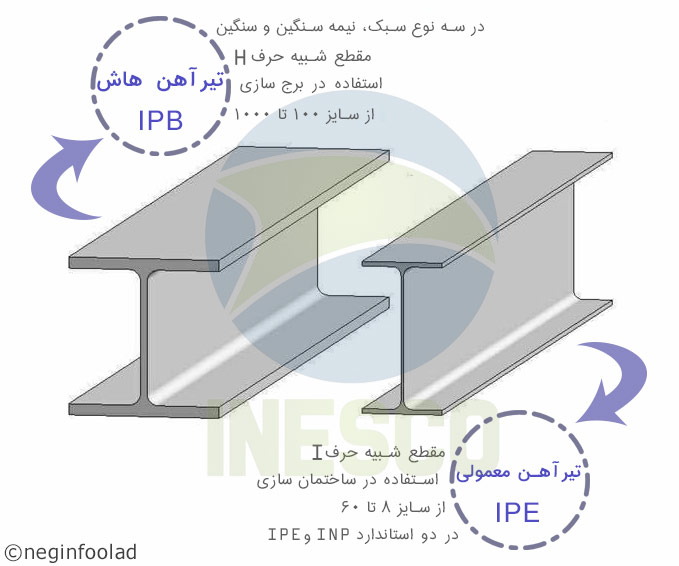
تفاوت تیرآهن هاش با تیرآهن معمولی
پر مصرف ترین سایز تیرآهن در کشور
تیرهای استاندارد IPE در ساختمان سازی از سایز 8 تا 60 دسته بندی می شوند. هرکدامیک از این سایزها دارای وزن متفاوتی می باشد. 8 ، 12 ، 14 ، 16 ، 18 ، 20 ، 22 ، 24 ، 27 و 30 سایزهای پرکاربردتری هستند. در میان این سایزها تیرآهن 14 بیشترین مصرف را در ساختمان سازی دارد.
به دلیل پهناور بودن کشورمان ایران، اغلب ساخت و سازها در ارتفاع محدودی انجام می شود و چون وزن زیادی بر روی سقف طبقه اول اعمال نمی شود اکثر سازندگان از سایز تیرآهن 14 استفاده می کنند. در برخی مواقع به جای استفاده از تیر 14 از پروفیل 140 در 140 استفاده می شود که به آن ستونی 14 گفته می شود. قیمت قوطی ستونی نیز بر اساس وزن و سایز آن ارزش گذاری می شود.

قوطی ستونی 14
قیمت تیرآهن 14
قیمت مقاطع فولادی هر روز و هر ساعت در حال نوسان است. میزان تولید کارخانجات، بهای جهانی آهن، بورس و قیمت دلار تاثیر بسیاری در نرخ گزاری آهن آلات دارد. برای دریافت آخرین قیمت تیرآهن 14 به صفحات مربوطه وبسایت و یا شماره های مندرج تماس حاصل فرمایید.
فولادهای ضد زنگ
فولادهای زنگ نزن
فولادهای ضد زنگ یا فولاد زنگ نزن یا استنلس استیل (Stainless Steel)، که Inox نیز خوانده میشود، آلیاژی از فولاد است که عناصر تشکیل دهنده آن ، آهن ( Fe )، کروم ( Cr ) و نیکل است که حداقل درصد جرمی کروم در آن ۱۰٫۵ درصد و حداکثر درصد جرمی کربن آن ۱٫۲ درصد است. حداقل درصد کروم نیز باید ۱۰٪ تا ۱۲٪ وزنی باشد.
در فولادهای زنگنزن علاوه بر کروم ( Cr ) عناصر آلیاژی دیگر نیز وجود دارد که عبارتند از: نیکل، مولیبدن، مس، تیتانیم، سیلیکون، منگنز، نایوبیم، آلومینیوم، نیتروژن و گوگرد.
فولاد زنگنزن به دلیل ویژگی غیرفعال شدن خود میتوانند مقاومت بسیار خوبی دربرابر خوردگی از خود نشان دهند. هرچه درصد کرین بیشتر باشد، مقاومت نسبت به خوردگی در فولادهای زنگنزن کمتر است.
انواع فولادهای ضد زنگ
1- فولاد زنگ نزن فریتی (Ferritic Stainless Steel)
نیکل عنصری گران قیمت است. فولادهای زنگ نزن فریتی حاوی 11.2 تا 19 درصد کروم هستند که ممکن است مقادیر بسیار کمی نیکل نیز به همراه داشته باشند. فولاد زنگ نزن فریتی نسبت به گریدهای حاوی نیکل بالا، مقرون به صرفه تر است. فولادهای زنگ نزن فریتی دارای خاصیت فرو مغناطیس هستند یعنی زمانی استفاده می شوند که شرایط خوردگی شدید نباشد، مانند ظروف پخت و پز آشپزی.
2- فولاد زنگ نزن مارتنزیتی (Martensitic Stainless Steel)
این دست از فولاد ها با عملیات آستنیته کردن و آبدهی ایجاد میشود. برای برخی کاربردها مقاومت به خوردگی، استحکام، مقاومت به سایش و داشتن لبه های تیز نیاز است ازازفولاد مارتنزیتی استفاده می کنند. به دلیل اینکه این نوع از فولاد ها فاقد نیکل هستند، آن را می توان ابتدا آهنگری نمود و سپس با آستنیته و سردکردن سریع (تشکیل مارتنزیت) و بازپخت دادن، عملیات حرارتی کرد.
از دیگر ویژگی های فولاد ضدزنگ مارتنزیتی خاصیت مغناطیسی است.
از فولاد زنگ نزن مارتنزیتی ، در ساخت پرههای توربین، تیغههای ریشتراش، لوازم جراحی استفاده می شود.
3- فولاد زنگ نزن آستنیتی (Austenitic Stainless Steel)
بزرگترین گروه فولادهای ضد زنگ، فولاد زنگ نزن آستنیتی است که دارای مقاومت به خوردگی، شکل پذیری و جوشپذیری عالی است. این نوع فولاد ها در شرایط خوردگی زیاد مورد استفاده قرار می گیرند. فولادهای ضد زنگ آستنیتی، در طیف گستردهای از کاربردها استفاده میشوند، از جمله: تزیینات داخلی خودرو ، تجهیزات آشپزی، غذایی و آشامیدنی، تجهیزات صنعتی.
4- فولاد زنگ نزن داپلکس ( Duplex stainless steels )
این دسته از فولادها دارای ساختار دو فازی هستند که از دانه های فولاد ضد زنگ فریتی و آستنیتی تشکیل شده اند. به همین دلیل داپلکس نامیده می شود. فولاد ضد زنگ داپلکس، در برابر خوردگی بسیار مقاوم است و جزو آلیاژهایی است که قابلیت سخت کاری دارند.
اگرچه فولاد ضد زنگ داپلکس قابلیت ماشین کاری دارد اما به دلیل استحکام بالا، ماشینکاری آن دشوار است. دربرای خوردگی مقاوم هستند و در محیطهای کلریدی و سولفیدی، هم مقاومت بسیار بالایی در برابر ترک ناشی از خوردگی تنشی از خود نشان میدهد.
از فولاد زنگ نزن داپلکس در مخازن تحت فشار، مبدل هاي حرارتي، تجهیزات کنترل آلودگی، شناسایی محل نفت و گاز و سکوهای دریایی استفاده می شود.
5- فولادهای پیر سخت شده
برای افزایش استحکام در آهن آلات روش های متعددی وجود دارد که یکی از مؤثرترین آنها ایجاد رسوب است. رسوبات با ایجاد مانع در برابر حرکت نا به جاییها ی موجود در شبکه بلوری ماده زمینه استحکام را افزایش میدهند. به این دست از فلزات فولادهای پیر سخت شده (Precipitation hardening) گفته می شود.
عملیات محلولسازی، سرد کردن سریع و تشکیل رسوب و پیرسازی سه مرحله تولید فولاد پیر سخت کاری شده است. از خواص مهم این فولاد عبارتاند از: سادگی ساخت، استحکام زیاد، شکل پذیری نسبتا خوب، و مقاومت به خوردگی عالی.